You might be surprised to learn that around 70% of all steel produced in the U.S. is recycled. Instead of being made from raw ore, most American steel is created by melting down scrap metal. This makes steel one of the most recycled and most cost-sensitive materials in the country. Factors like export volume and weather can influence availability and pricing. For example, during winter months, scrap collection slows because much of it is buried under snow and ice. Less scrap means tighter supply and higher prices.
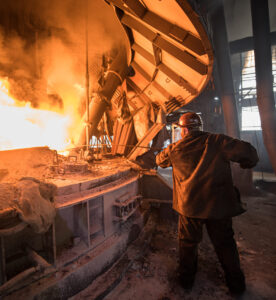
Where Amramp Sources Our Steel
Once the steel is produced, we source it in two ways: directly from mills and through local distributors.
For large orders, we go straight to the mill to get the best pricing. We frequently work with Nucor, one of the largest steel producers in the U.S., for these bulk purchases.
For smaller quantities or specialized materials, we turn to trusted distributors who buy in massive volume. This allows us to benefit from their bulk purchases without needing to place massive orders ourselves. Our distributor network includes companies in New Bedford, Marlborough, Massachusetts
We’ve also partnered with a company based out of Baltimore, Maryland for over 16 years, sourcing the steel tubing used in our handrails. Our walking surfaces—called expanded metal mesh—come from manufacturers in Oklahoma and, previously, Quebec (though less so now due to uncertainty around tariffs).
From Steel to Ramp: The Production Process
Once the steel arrives at our facility, we will immediately begin turning it into ramp components. Our franchisees keep an onsite inventory in their local warehouses, so our shop operates continuously, allowing us to keep all standard parts in stock and fulfill orders without delay. We produce and stock over 100 unique parts to ensure fast delivery.
Here’s how the process works:
- Receiving and Staging Materials: A 53-foot trailer backs into our facility under a massive crane. The crane unloads raw steel and either stores it or moves it directly into production.
- Cutting and Hole Punching: Each 20-foot steel stick is fed into a pre-programmed CNC machine that cuts it to the correct length and punches holes in a precise pattern. These parts are grouped into kits—each kit is used to create 28 modular ramp sections or 24 platforms.
- Frame Welding: Our welding team fabricates the steel frames using the kits. A single kit typically produces 28 welded sections, which form the structural backbone of our ramp systems.
- Mesh Installation: Each welded frame is matched with a corresponding expanded metal mesh to create what we call an “assembly”—a complete ramp section.
New in 2024: Thanks to a grant from the MMAP Program, we’ve introduced robotic welding into this process. Our new welding robot automates both the frame welding and mesh installation steps, improving precision and output.
- Powder Coating: Each finished assembly moves onto our powder coating line:
- Parts are hung on a conveyor track
- They undergo a three-stage chemical wash, rinse, and seal
- After washing, they’re dried at 300°F+, powder-coated, baked to cure the finish, and cooled
- Once complete, they’re ready for shipping
- Packaging and Shipping: As assemblies cool, they arrive at the shipping department, where they’re organized by part and matched to customer orders. The team then picks, packs, and ships the required components quickly and efficiently.
- Final Assembly in the Field: Franchisees maintain their own local stock of parts, allowing them to respond immediately when a customer needs a ramp. Once on-site, they assemble the necessary configuration using our modular components—providing access and empowering independence in just a few hours.
Why It Matters
Our system is built for speed, scale, and reliability. From sourcing recycled steel to keeping over 100 parts in stock, we’ve designed our process to ensure fast response times and consistent quality. Whether it’s a single ramp or a large installation, you can count on Amramp to deliver a durable, American-made solution, ready to go when you need it.
Need a ramp? Now you know exactly how it’s made.